The Role of Servo Hydraulic Presses in Automotive Manufacturing
In the fast-paced world of automotive manufacturing, precision, and efficiency are paramount. Servo hydraulic presses have emerged as a game-changer, revolutionizing the production of automotive components. This blog post explores how servo hydraulic press are used in automotive manufacturing, their benefits, and how they shape the industry's future. Whether you're a seasoned industry professional or new to automotive manufacturing, this guide will provide valuable insights into the role of servo hydraulic presses in achieving consistent quality and efficiency.
Table of contents:
How Hydraulic Presses Are Used in Automotive Component Production
The Benefits of Servo Hydraulic Presses in Achieving Consistent Quality
Case Studies: Successful Implementation of Servo Presses in Automotive Plants
How Servo Press Technology Is Shaping the Future of Automotive Manufacturing
How Hydraulic Presses Are Used in Automotive Component Production
Hydraulic presses are essential tools in the automotive industry, used for various applications such as forging, molding, and stamping. These presses apply a controlled amount of force to shape metal and composite materials into intricate automotive parts, ensuring high precision and repeatability. From forming car body panels to producing engine components, hydraulic presses play a crucial role in manufacturing robust and reliable automotive parts.
The Benefits of Servo Hydraulic Presses in Achieving Consistent Quality
Servo hydraulic presses combine the best of hydraulic and servo technologies, offering unparalleled control and precision. Unlike traditional hydraulic presses, servo hydraulic presses use a servo motor to control the press's movement, providing real-time feedback and adjustments. This results in consistent and repeatable quality, reducing the risk of defects and improving overall production efficiency. Additionally, servo hydraulic presses are energy-efficient, reducing power consumption and operating costs.
Case Studies: Successful Implementation of Servo Presses in Automotive Plants
Several automotive manufacturers have successfully integrated servo hydraulic presses into their production lines, reaping significant benefits. For instance, a leading car manufacturer in Germany implemented servo hydraulic presses to produce high-strength steel components, resulting in a 20% increase in production efficiency and a 15% reduction in material waste. Another example is an American automotive plant that used servo presses to manufacture aluminum body panels, achieving a 25% improvement in dimensional accuracy and a 10% reduction in production time.
How Servo Press Technology Is Shaping the Future of Automotive Manufacturing
The future of automotive manufacturing is increasingly reliant on advanced technologies like servo hydraulic presses. These presses enable manufacturers to produce lighter, stronger, and more complex components, aligning with the industry's trend toward electric and autonomous vehicles. By leveraging servo press technology, automotive manufacturers can stay competitive, reduce environmental impact, and meet the growing demand for high-quality, innovative vehicles.
Servo hydraulic presses are transforming automotive manufacturing, offering unmatched precision, efficiency, and quality. By understanding and harnessing the power of servo press technology, automotive manufacturers can achieve significant improvements in their production processes, ensuring they remain at the forefront of the industry. To learn more about integrating servo hydraulic presses into your manufacturing operations, explore further resources or contact a specialized supplier today.
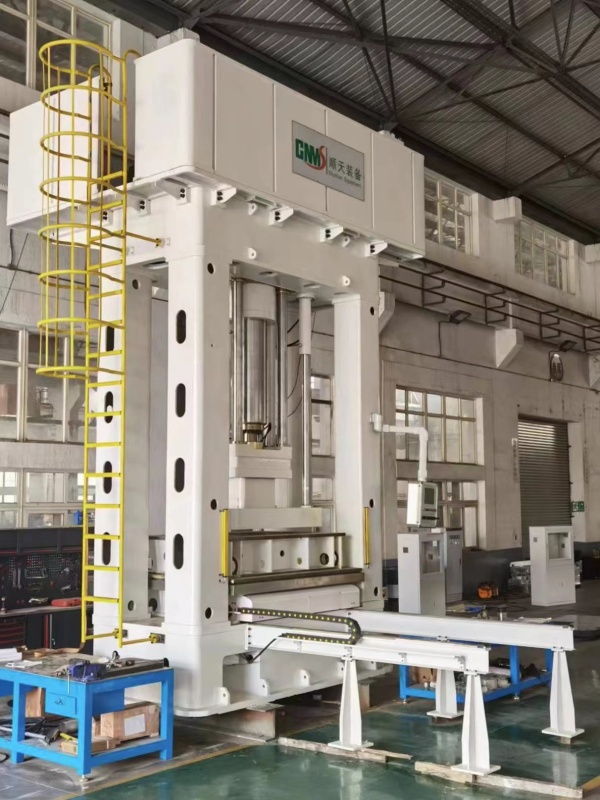
Comments
Post a Comment