A Deep Dive into Double Cooling Channel Cold Plates for Diode Modules
In the rapidly evolving world of electronics, efficient thermal management is crucial for device performance and longevity. One innovation gaining traction is the double cooling channel cold plate, especially for diode modules. These advanced cooling solutions showcase the seamless integration of engineering and technology, offering remarkable benefits for industries reliant on precision cooling. In this blog post, we explore the advantages of double cooling channel designs, the role of CNC machining parts in enhancing cooling performance, and the importance of selecting the right manufacturer for your cooling needs.
Table of contents
Benefits of Double Cooling Channel Designs in CNC-Machined Cold Plates
How CNC Precision Enhances Cooling Performance in Diode Modules
Choosing the Right CNC Cold Plate Manufacturer for Optimal Thermal Management
Benefits of Double Cooling Channel Designs in CNC-Machined Cold Plates
The introduction of double cooling channel designs in CNC-machined cold plates has revolutionized thermal management in modern electronics. These designs offer enhanced cooling efficiency, which is vital for high-performance diode modules. By incorporating parallel cooling paths, double channel designs ensure that heat is dissipated more evenly across the plate’s surface. This reduces the thermal resistance, allowing for a more uniform temperature distribution and preventing hot spots that could potentially damage sensitive components. Another significant advantage of double cooling channel designs is their ability to increase the flow rate of the coolant without significantly raising the pressure drop. This balance is crucial for optimizing the cooling performance while maintaining energy efficiency. The reduced pressure drop results in less stress on the pumping systems, extending their lifespan and reducing maintenance costs. Furthermore, the design enables greater flexibility in the choice of coolants, ranging from water-based solutions to specialized fluids, each catering to specific cooling requirements and environmental considerations.
How CNC Precision Enhances Cooling Performance in Diode Modules
CNC machining plays a pivotal role in the manufacturing of double cooling channel cold plates, ensuring precision and high-quality output. The process allows for the intricate cutting and shaping of materials, which is essential for creating the complex geometry of cooling channels. CNC machining offers unparalleled accuracy, which is crucial for maximizing the contact surface area between the cold plate and the diode module. This increased contact area improves heat transfer efficiency, leading to superior cooling performance. The precision of CNC machining also contributes to the uniformity and consistency of the cooling channels. Consistent channel dimensions ensure that the coolant flows smoothly throughout the cold plate, minimizing turbulence and optimizing heat dissipation. Additionally, CNC machines can work with a variety of materials, including aluminum and copper, which are commonly used in cold plate fabrication due to their excellent thermal conductivity and lightweight properties.
Choosing the Right CNC Cold Plate Manufacturer for Optimal Thermal Management
Selecting the right CNC cold plate manufacturer is a critical step in achieving effective thermal management for diode modules. With so many options available, it is essential to evaluate manufacturers based on their expertise, technology, and track record in the industry. One of the key factors to consider is the manufacturer's experience in designing and producing cold plates with double cooling channel designs. An experienced manufacturer will have a deep understanding of the intricacies involved in optimizing thermal performance and can provide valuable insights during the design phase. Another important consideration is the manufacturing capabilities and technologies used by the manufacturer. State-of-the-art CNC equipment and advanced software tools are essential for producing high-quality cold plates with precise geometries and tight tolerances. Manufacturers that invest in cutting-edge technology are better equipped to deliver consistent quality and innovative solutions that meet the evolving demands of the industry.
In conclusion, the implementation of double cooling channel cold plates in diode modules represents a significant advancement in thermal management technology. By understanding the benefits of these designs, the role of CNC machining, and the importance of choosing the right manufacturer, businesses can harness the full potential of this innovation. For those looking to integrate these solutions into their operations, collaboration with experienced CNC machining manufacturers is key to unlocking optimal performance and reliability in their thermal management systems.
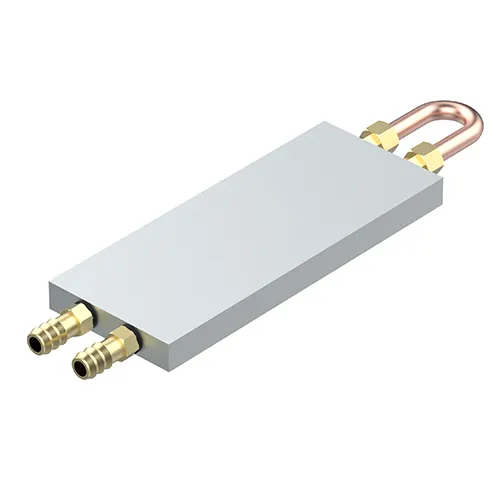
Comments
Post a Comment