Creative Ways to Maximize Your CNC Machining Service Budget
Navigating the world of CNC machining services can feel like a balancing act. On one hand, you want high-quality, custom CNC service products that meet your specific needs. On the other, you need to keep costs under control. But fear not! This guide is designed to help you unlock cost-effective strategies for utilizing CNC machining services.Understanding how to optimize your design, choose the right materials, and develop strong supplier relationships can save you money while delivering the quality you need. Let's explore these strategies in detail.
Table of contents:
Optimizing Design for Manufacturability
Selecting Appropriate Materials for Cost Efficiency
Batch Production vs. On-Demand Manufacturing
Leveraging Supplier Relationships for Better Pricing
Optimizing Design for Manufacturability
When it comes to reducing costs in CNC machining, design is king. Designing with manufacturability in mind means creating parts that are easier and cheaper to produce. A few tweaks to your design can make a big difference in overall costs.First, consider simplifying your design. Complex designs often require more complex, multi-axis CNC machines, which can drive up costs. Opting for simpler shapes and fewer intricate details can lower manufacturing costs significantly. Additionally, using standard sizes and features in your design can reduce the need for custom CNC service adjustments, saving time and money.Secondly, think about the tolerances you set. While tight tolerances are sometimes necessary, they can also increase machining time and cost. Assess if looser tolerances could work for your project without compromising functionality.Lastly, prepare a comprehensive design brief for your CNC cutter tool manufacturer. This not only ensures you receive an accurate quote but also helps avoid costly revisions down the road.
Selecting Appropriate Materials for Cost Efficiency
Choosing the right materials is another essential strategy for minimizing CNC machining costs. Material selection affects both the machining process and the final product, so it's crucial to weigh your options carefully.Consider the properties required for your application. While premium materials may offer superior performance, they can also be expensive. Instead, identify materials that meet your strength, durability, and weight requirements without breaking the bank. For instance, aluminum is often a cost-effective alternative to more expensive metals.Additionally, explore the use of composite materials that combine different properties at a lower cost. These materials can offer significant savings while maintaining the necessary performance standards for your project.Finally, consult with your CNC machining service provider to get their input on material choices. Their expertise can provide valuable insights that lead to more economical choices.
Batch Production vs. On-Demand Manufacturing
Deciding between batch production and on-demand manufacturing can also impact your CNC machining costs. Each approach has its advantages depending on your specific needs and project timeline.Batch production involves manufacturing multiple units at once, which can result in lower per-unit costs due to economies of scale. This approach is often ideal for projects with consistent demand and large order quantities.On-demand manufacturing, on the other hand, focuses on producing smaller quantities as needed. This method can reduce storage costs and minimize waste but may come with higher per-unit costs. It's a good fit for projects with fluctuating demand or limited initial capital.Evaluate your project requirements to determine which approach suits your needs best. Consider factors like order volume, financial constraints, and delivery schedules when making your decision.
Leveraging Supplier Relationships for Better Pricing
Building strong relationships with your CNC machining service suppliers can lead to better pricing and improved service. Open communication and collaboration can help you negotiate favorable terms and secure discounts.Start by choosing a reliable supplier with a proven track record. Look for a partner who understands your industry and can offer tailored solutions. A supplier who is invested in your success will be more open to discussing cost-saving opportunities.Regularly share your business goals and production forecasts with your supplier. This transparency allows them to anticipate your needs and adjust their processes accordingly, potentially resulting in cost savings.Lastly, consider consolidating your orders with a single supplier. This can increase your bargaining power and enable you to negotiate volume discounts or preferential rates.
Cost-effective CNC machining doesn't mean cutting corners. By optimizing your design, selecting the right materials, choosing the appropriate production method, and leveraging supplier relationships, you can achieve high-quality results without overspending. Implement these strategies in your next custom CNC service project to maximize your budget and enjoy superior results.For more in-depth guidance and expert advice, consider reaching out to CNC machining service professionals who can help tailor these strategies to your specific needs.
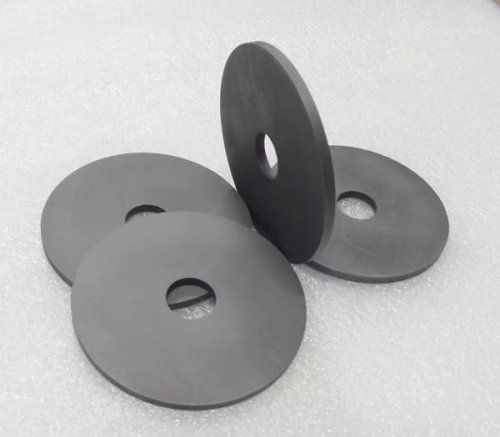
Comments
Post a Comment