Hot Press Forming for Fuel Cell MEA Production: Techniques and Benefits
In the rapidly advancing world of fuel cell technology, innovation continues to drive efficiency and performance. One such advancement is hot press forming, a technique at the forefront of fuel cell membrane electrode assembly (MEA) production. This blog explores the importance of hot press forming for fuel cell electric vehicles, its benefits, and how it enhances production quality. For those invested in cutting-edge technology and sustainability, understanding hot press forming technology could be pivotal in optimizing operations.
Table of contents:
Key Advantages of Using Hot Press Technology for Fuel Cell Performance
How Hot Press Forming Improves Efficiency and Reduces Defects in MEA Layers
Tips for Selecting Hot Press Equipment for Reliable Fuel Cell MEA Quality
Why Hot Press Forming Ensures Consistency in Fuel Cell MEA Production
Hot press forming offers unparalleled consistency in the production of fuel cell MEA layers. With precise control over both pressure and temperature, this method guarantees uniformity across all units. This precision is crucial for maintaining the integrity of the MEA, which directly affects the performance and reliability of fuel cells in electric vehicles. By standardizing the process, manufacturers can minimize variations and ensure each fuel cell operates at optimal efficiency, providing a competitive edge in the market.
Key Advantages of Using Hot Press Technology for Fuel Cell Performance
The key advantage of hot press forming technology lies in its ability to produce high-performance MEA layers with minimal defects. The process allows for the even distribution of materials, resulting in improved conductivity and reduced ohmic resistance within the MEA. This not only enhances the overall efficiency of the fuel cell but also extends its operational lifespan. Furthermore, the technology supports the integration of advanced materials, paving the way for next-generation fuel cells that promise greater power output and sustainability.
How Hot Press Forming Improves Efficiency and Reduces Defects in MEA Layers
Efficiency and quality control are critical in the production of MEA layers, where even minor defects can lead to significant performance issues. Hot press forming addresses these challenges by providing a controlled environment that reduces the likelihood of defects. Enhanced by servo-electric systems, the precision delivery of heat and pressure ensures that each layer is perfectly formed, eliminating inconsistencies. This results in MEA layers that are not only robust but also perform consistently under various operating conditions.
Tips for Selecting Hot Press Equipment for Reliable Fuel Cell MEA Quality
Selecting the right hot press equipment is vital for achieving reliable fuel cell MEA quality. When evaluating options, consider machinery that offers advanced servo-electric controls, as these provide superior accuracy for pressure and temperature management. Additionally, equipment that features customizable settings can accommodate different material specifications, offering flexibility in production. Investing in high-quality machinery with proven track records in fuel cell applications will ensure that your production process remains efficient and yields top-tier MEA quality.
In conclusion, hot press forming stands out as a transformative technology in the production of fuel cell MEAs. By delivering precision, consistency, and enhanced performance, this method not only optimizes the efficiency of electric vehicle fuel cells but also sets the stage for future advancements and innovations. As the demand for sustainable energy solutions grows, the adoption of hot press forming in MEA production will likely become a cornerstone for the industry. Manufacturers looking to remain competitive and lead in performance-driven technologies should embrace this technique to meet the evolving needs of the market. Emphasizing quality and sustainability, hot press forming is poised to play a crucial role in the evolution of fuel cell technologies.
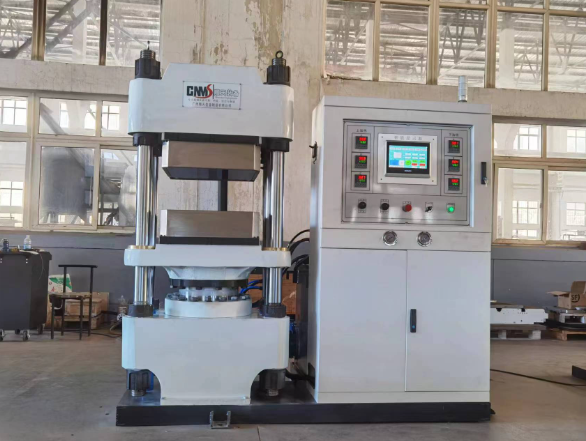
Comments
Post a Comment