Revolutionizing Textile Production with Circular Knitting Machine Sinkers
In the rapidly evolving textile industry, the role of machine components in enhancing fabric quality and production efficiency cannot be overstated. Circular knitting machines, central to this industry, are experiencing significant innovations, particularly in their circular knitting machine sinkers.
Table of contents:
The Evolution of Sinker Design in Modern Circular Knitting Machines
How High-Performance Circular Knitting Machine Sinkers Improve Knitting Speed and Precision
The Role of Circular Knitting Machine Sinkers in Reducing Fabric Defects and Waste
These small yet crucial parts are transforming how textiles are produced, improving both the speed and quality of fabric manufacturing. For manufacturers and textile producers, understanding these advancements is essential for staying competitive and meeting the growing demands for high-quality fabric.
The Evolution of Sinker Design in Modern Circular Knitting Machines
The textile industry has witnessed remarkable technological advancements over the years. Among these, the evolution of sinker design in circular knitting machines stands out as a pivotal development. In the past, sinkers were simple components, designed primarily to hold the yarn in place during the knitting process. However, High-Performance Circular Knitting Machine sinkers are engineered with precision, offering enhanced functionality and efficiency. Today's sinkers are crafted with cutting-edge materials and designs, allowing manufacturers to produce fabrics with greater consistency and fewer defects. This evolution has been driven by the need to meet consumer demand for high-quality textiles, as well as the industry's push towards more sustainable and efficient manufacturing processes. The transformation in sinker design has also been influenced by advancements in materials science. High-Performance Circular Knitting Machine sinkers are often made from high-strength alloys and coated with protective layers that reduce wear and tear. This not only extends the lifespan of the sinkers but also enhances the overall efficiency of the circular knitting machines.
How High-Performance Circular Knitting Machine Sinkers Improve Knitting Speed and Precision
High-performance circular knitting machine sinkers are revolutionizing the way textiles are produced by significantly enhancing knitting speed and precision. These advanced sinkers are designed to optimize the interaction between the yarn and the machine, allowing for faster production cycles without compromising on quality. By reducing friction and ensuring smooth yarn movement, these sinkers enable machines to operate at higher speeds, meeting the demands of large-scale textile production. This is particularly beneficial for manufacturers looking to increase output and reduce production time, ultimately leading to cost savings and improved profitability. In addition to speed, precision is a critical factor in textile production. High-performance sinkers are meticulously engineered to maintain consistent loop formation, which is essential for producing uniform and high-quality fabrics. This precision is achieved through the use of advanced materials and manufacturing techniques, ensuring that the sinkers can withstand the rigors of high-speed knitting. The result is a seamless knitting process that minimizes the risk of defects, such as skipped stitches or irregular patterns, which can compromise the integrity of the final product.
The Role of Circular Knitting Machine Sinkers in Reducing Fabric Defects and Waste
In the quest for sustainable textile manufacturing, reducing fabric defects and waste is paramount. Circular knitting machine sinkers play a crucial role in achieving this goal by enhancing the precision and consistency of the knitting process. By ensuring accurate loop formation and maintaining uniform tension throughout the fabric, these sinkers minimize the occurrence of defects such as holes, runs, and uneven patterns. This not only improves the quality of the finished product but also reduces the amount of waste generated during production, contributing to a more sustainable manufacturing process. The reduction of fabric defects is closely linked to the advanced design and materials used in High-performance circular knitting machine sinkers. These components are crafted to withstand the demands of high-speed knitting while maintaining their integrity over extended periods. The use of durable materials and precision engineering ensures that the sinkers can operate at optimal efficiency, reducing the likelihood of mechanical failures that can lead to fabric defects. This reliability is crucial for manufacturers aiming to produce high-quality textiles consistently and efficiently.
The innovations in circular knitting machine sinkers are transforming the textile industry, offering significant improvements in efficiency, fabric quality, and sustainability. By enhancing the speed and precision of knitting processes, these advanced components are helping manufacturers meet the demands of a competitive market while reducing waste and environmental impact. For textile producers and circular knitting machine sinker manufacturers, investing in High-performance circular knitting machine sinkers is a strategic decision that can drive growth and ensure long-term success. By staying informed about the latest advancements in sinker design and technology, companies can position themselves at the forefront of the industry, ready to capitalize on new opportunities and challenges.
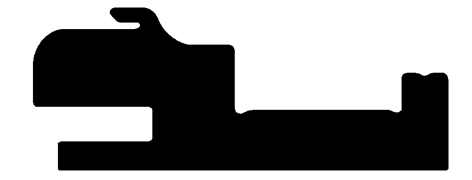
Comments
Post a Comment