The Benefits of Using Induction and Vacuum Melting Furnaces
Induction and vacuum melting furnaces play a critical role in modern metallurgical processes. These furnaces are designed to produce high-quality metals and alloys with exceptional purity and uniformity, meeting the exacting standards of industries such as aerospace, medical, and automotive manufacturing. By utilizing advanced melting techniques, induction and vacuum melting furnaces offer numerous advantages, including precise temperature control, reduced contamination, and improved energy efficiency. This introduction explores their benefits and significance in industrial applications.
Table of contents:
How Induction Melting Machines Enhance Efficiency and Reduce Energy Costs
Why Vacuum Induction Melting Furnaces Are Ideal for High-Purity Metals
The Role of Small Vacuum Induction Furnaces in Custom Metal Production
How Induction Melting Machines Enhance Efficiency and Reduce Energy Costs
Induction and vacuum melting furnaces have revolutionized metal smelting and casting, offering unparalleled precision and efficiency for industries requiring high-purity metals. High Vacuum Melting Furnace Manufacturer like Taeantech provide cutting-edge solutions that cater to industries such as aerospace, electronics, and fine metallurgy. These advanced systems allow the melting and casting of metals, including platinum, gold, copper, and various alloys, under controlled environments that eliminate common impurities and losses associated with traditional methods. For instance, Taeantech's 1-30kg High Vacuum Melting Furnace leverages German-engineered vacuum pumps to achieve a vacuum degree of up to 10^-2 Pa, ensuring molten metals remain shielded from air exposure. The inclusion of an IGBT high-frequency induction heating device enables rapid heating up to 2200°C within minutes, allowing even high-temperature-resistant metals like platinum and palladium to be processed with remarkable speed and efficiency. Additionally, the intelligent Mitsubishi PLC+PID control systems simplify operations, offering users a clear interface and precise temperature management with deviations as low as ±1°C, making these high-tech furnaces indispensable for businesses aiming for precision and quality.
Why Vacuum Induction Melting Furnaces Are Ideal for High-Purity Metals
Copper melting furnace, like Taeantech's small vacuum induction models, are revolutionizing industries by optimizing production and reducing energy costs. These furnaces heat copper directly, minimizing waste while ensuring efficiency. With one-key operation systems and options for manual or automated pouring, they streamline workflows and maintain material integrity. Designed for small-scale or custom copper production, they support secondary feeding and mechanical stirring under vacuum, resulting in uniform composition without segregation or porosity. This ensures durable, high-quality copper products, whether for industrial use or fine-crafted items. Combining efficiency, safety, and cost-effectiveness, these furnaces are essential for competitive production.
The Role of Small Vacuum Induction Furnaces in Custom Metal Production
Vacuum induction melting furnaces, particularly small-scale versions, play a critical role in industries demanding high-purity metal production, offering a blend of innovation and precision. Taeantech's TAKJ-HVQ series furnaces underline these benefits with features like high-speed melting times (e.g., 30kg of gold in just five minutes) and intelligent process control, catering to both large and small-scale needs. By isolating molten metals from the atmosphere using inert gases like argon or nitrogen, vacuum furnaces eliminate oxidation to protect materials, making them an excellent investment for high-quality production. Furthermore, advanced mechanical stirring functions and secondary feeding options contribute to creating defect-free, homogenous products, which are vital for manufacturers catering to industries with stringent material requirements like aerospace and electronics. The robust infrastructure of these furnaces, from their German-engineered vacuum systems to their intelligent interfaces, ensures consistent performance and minimal downtime. If you're exploring top-tier solutions for metal melting and casting, consider a High Vacuum Melting Furnace Manufacturer such as Taeantech, known for its reliable and efficient equipment suited to diverse industrial demands. Whether you're producing intricate jewelry, gold bullion, or industrial-grade metal components, the right furnace technology ensures your process meets the highest standards of precision and efficiency.
In conclusion, selecting the right High Vacuum Melting Furnace Manufacturer is crucial for achieving optimal results in metal melting and casting processes. Advanced furnace technology not only enhances precision and efficiency but also ensures compliance with the rigorous demands of modern industries. Companies like Taeantech exemplify the innovation and reliability necessary to meet diverse production needs. By investing in state-of-the-art equipment, manufacturers can ensure the consistency, quality, and performance required to excel in competitive markets.
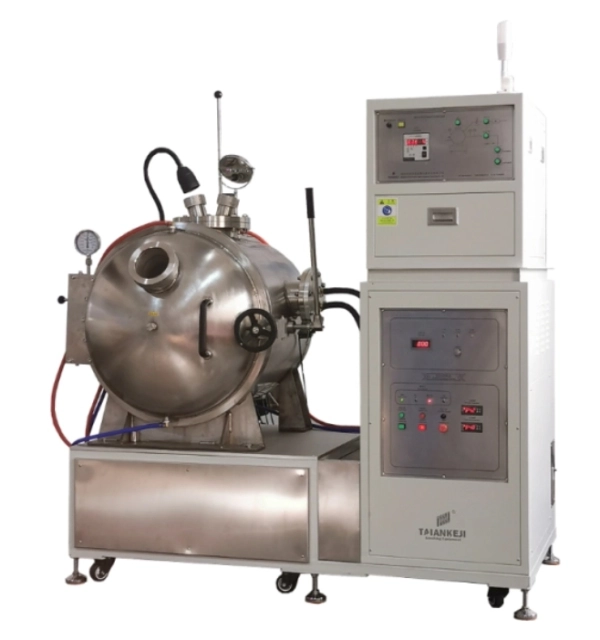
Comments
Post a Comment