Understanding Cemented Carbide Components and Their Industrial Applications
Cemented carbide components are among the most widely used materials in modern industries due to their extraordinary hardness, wear resistance, and versatility. These components have transformed manufacturing processes and boosted the efficiency of numerous applications. Whether you are using cemented carbide inserts for precision cutting or tough industrial tooling, this material leads the way in durability and reliability. This blog dives into the composition, manufacturing processes, benefits, and industries where cemented carbide makes a significant impact.
Table of contents:
The Composition and Manufacturing Process of Cemented Carbide
Key Industries Utilizing Cemented Carbide Components
Advantages of Cemented Carbide in High-Wear Environments
Comparing Cemented Carbide to Other Hard Materials
The Composition and Manufacturing Process of Cemented Carbide
Cemented carbide, often referred to as tungsten carbide, is a composite material that combines tungsten carbide particles with a metallic binder, typically cobalt or nickel. This blend is created through a sintering process, where the powdered materials are heated in a controlled environment, allowing them to bond and form a dense, durable material. The result is a substance with high hardness, capable of withstanding extreme conditions. Industries can use these components in demanding settings, especially when paired with advanced coating technologies like CVD (Chemical Vapor Deposition) or PVD (Physical Vapor Deposition). These coatings enhance wear resistance, heat dissipation, and tool life, making cemented carbide components suitable for cutting, drilling, and high-speed operations.
Key Industries Utilizing Cemented Carbide Components
Cemented carbide components have applications across a broad range of industries. Manufacturing sectors rely heavily on carbide inserts for milling, turning, and drilling operations. The automotive and aerospace industries utilize these materials for precision machining and durable cutting tools. Additionally, cemented carbide is vital in the mining industry, where it is used in high-impact tools like drill buttons and insert bits. CNC cutting tools that incorporate cemented carbide provide unmatched performance for professional tube production, as seen in products like the SHARPLY tube scraper inserts. These advanced tools remove imperfections and ensure smoother finishes on pipes, proving how indispensable carbide technologies have become.
Advantages of Cemented Carbide in High-Wear Environments
The unparalleled properties of cemented carbide make it the material of choice for high-wear environments. Its exceptional hardness allows it to outlast traditional materials under extreme stress, reducing the need for frequent tool replacements. This longevity increases production efficiency by minimizing downtime and maintenance costs. Furthermore, the material's high melting point and chemical resistance make it stable under intense heat and corrosive conditions. Cemented carbide inserts, used in CNC machines or industrial tooling, deliver consistent performance even in demanding operations, proving their worth in both small-scale tasks and large-scale industrial applications.
Comparing Cemented Carbide to Other Hard Materials
When placed alongside other hard materials, such as high-speed steel or ceramics, cemented carbide reigns supreme. High-speed steel tools, while highly affordable, lack the durability and strength inherent to cemented carbide. Similarly, ceramics are brittle and prone to chipping under impact, making them less suitable for heavy-duty operations. Cemented carbide inserts offer a unique balance of toughness and wear resistance that other materials cannot replicate, providing superior performance for various industrial applications. Its versatility extends further with customizable designs, such as rods, blanks, or scraper inserts, catering to specific operational requirements and producing exceptional outcomes.
Cemented carbide has undeniably revolutionized modern industries with its superior qualities, ensuring optimal performance in high-wear and precision-demanding environments. If your processes can benefit from cemented carbide tools, it's crucial to integrate products like cemented carbide inserts into your operations to achieve unparalleled efficiency, cost savings, and performance results.
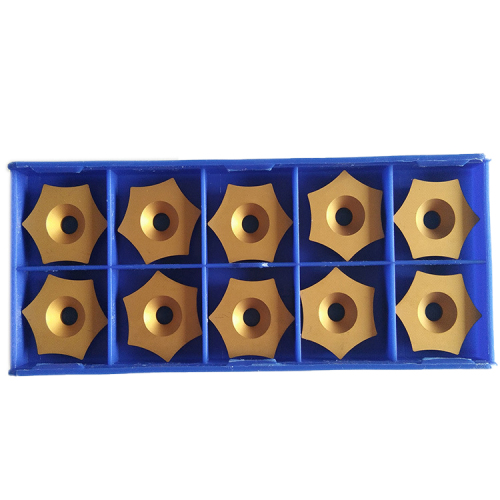
Comments
Post a Comment