Understanding the Manufacturing Standards of Tungsten Carbide Rods
Tungsten carbide rods are essential components in various industries due to their exceptional hardness, wear resistance, and durability. Whether used in cutting tools, drills, or other specialized applications, these rods need to meet stringent manufacturing standards to deliver optimal performance. This blog explores the critical factors that define reliable tungsten carbide rods supplier, the importance of premium alloys, the impact of precise engineering, and the role of international compliance in ensuring top-quality solid tungsten carbide rods.
Table of contents:
Key Factors That Set Reliable Tungsten Carbide Rods Suppliers Apart
Exploring the Use of Premium Alloys in Solid Tungsten Carbide Rods
The Impact of Precise Engineering on Tool Durability and Efficiency
Ensuring Compliance With International Manufacturing Standards
Key Factors That Set Reliable Tungsten Carbide Rods Suppliers Apart
Choosing the right tungsten carbide rods supplier is crucial for industries that rely on the consistent quality of these high-performance materials. Reliable suppliers stand out for their commitment to precision manufacturing, use of cutting-edge equipment, and ability to provide customized solutions aligned with industry demands. Many trustworthy tungsten carbide rods suppliers invest heavily in quality control measures throughout the production process. From raw material selection to the final inspection of the rods, these measures ensure consistency and adherence to client specifications. Furthermore, top suppliers place equal emphasis on customer service, ensuring timely deliveries and offering technical support to address specific application needs. These attributes make a significant difference to customers searching for dependable tungsten carbide rods suppliers.
Exploring the Use of Premium Alloys in Solid Tungsten Carbide Rods
The foundation of exceptional solid tungsten carbide rods lies in the alloys used during manufacturing. High-grade tungsten carbide mixed with precision-bonded cobalt or nickel binders ensures these rods possess the strength and stiffness demanded by complex industrial applications. Tungsten carbide alloys are specifically engineered to offer enhanced wear resistance and toughness, enabling the rods to withstand extreme pressure and temperature conditions without compromising their structural integrity. Premium alloys also result in superior machinability, meaning tools fashioned from solid tungsten carbide rods can achieve fine detailing with minimal risk of breakage. Customers looking for a tungsten carbide rods supplier should inquire about the quality and type of alloys being used, as this directly impacts the efficiency and lifespan of the final product.
The Impact of Precise Engineering on Tool Durability and Efficiency
One of the defining characteristics of high-quality tungsten carbide rods is the precision with which they are engineered. During manufacturing, processes such as extrusion, sintering, and grinding must be meticulously monitored to achieve uniform density and flawless surface finishes in the final rods. Precise engineering directly affects tool durability, ensuring that the solid tungsten carbide rods used in drills or cutters maintain sharpness and resistance to abrasion over extended periods. Accurate dimensional tolerances are another factor that enhances the overall efficiency of tools crafted from these rods, reducing the chance of premature tool failure and ensuring seamless performance in various industrial settings. Potential buyers should evaluate a tungsten carbide rods supplier not only on the quality of materials but also on their engineering expertise to achieve these precise outcomes.
Ensuring Compliance With International Manufacturing Standards
For manufacturers of tungsten carbide rods, ensuring compliance with international standards is paramount. Reputable tungsten carbide rods suppliers adhere to ISO certifications and other relevant regulatory frameworks, which guarantee uniformity, safety, and sustainability in their production processes. Each solid tungsten carbide rod undergoes rigorous testing to verify its hardness, tensile strength, and temperature resistance, ensuring it meets the required benchmarks for industrial use. Compliance also includes adopting environmentally friendly practices, such as minimizing waste and using responsibly sourced raw materials. Companies that prioritize adherence to these standards provide customers with the assurance of purchasing products that meet global quality expectations, making them preferred choices for industries around the world.
Tungsten carbide rods have become indispensable in modern manufacturing, offering unparalleled durability, strength, and versatility for a wide range of industrial applications. By selecting reputable suppliers who adhere to international standards and prioritize quality, businesses can ensure optimal performance and reliability in their operations. The combination of advanced engineering, rigorous testing, and sustainable practices makes tungsten carbide rods a trusted solution for industries striving for excellence. Ultimately, investing in high-quality tungsten carbide rods is a step towards efficiency, precision, and long-term success.
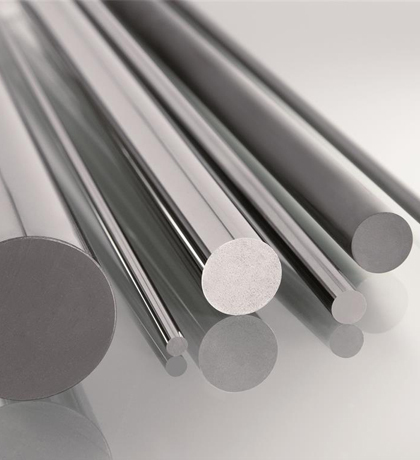
Comments
Post a Comment