The Science Behind Zinc Plating Intermediates and Their Impact on the Process
In the world of metal finishing, electroless zinc plating plays a vital role in protecting various materials from corrosion and enhancing their aesthetic appeal. While the basic principles of zinc plating are well-established, the intricacies of achieving a high-quality, durable, and uniform coating often rely on the strategic use of zinc plating intermediates. These seemingly small components within the plating bath can dramatically influence the outcome of the plating process. This blog post will explore the crucial role of these intermediates and how they contribute to superior zinc plating results.
Table of contents:
Understanding Zinc Plating Intermediates in Electroplating:
How Zinc Plating Intermediates Improve the Coating Process:
The Role of Intermediates in Achieving a Uniform Zinc Coating:
Understanding Zinc Plating Intermediates in Electroplating:
Zinc plating intermediates are carefully selected chemical compounds added to the zinc plating solution to modify and optimize the plating process. These aren't just passive ingredients; they actively participate in the electrochemical reactions occurring at the cathode (the part being plated). The choice of specific intermediates depends heavily on the type of plating bath being used – whether it's an acid zinc plating bath, an alkaline zinc plating bath, or even a zinc-nickel alloy plating bath. For example, certain intermediates are specifically designed to enhance the throwing power of the plating bath, allowing zinc to deposit more evenly in recessed areas and complex geometries. This is particularly important when plating thin steel sheets, as mentioned in materials like those offered by FengFanTrade (referencing their acid zinc plating electroplating chemicals for thin steel sheet).
How Zinc Plating Intermediates Improve the Coating Process:
The addition of carefully chosen zinc plating intermediates can significantly improve several aspects of the zinc coating. One key benefit is grain refinement. Intermediates can promote the formation of smaller, more uniform zinc crystals during the plating process. This results in a smoother, denser, and more visually appealing coating. Furthermore, specific intermediates can enhance the brightness and leveling properties of the zinc deposit, leading to a higher gloss finish and reduced surface roughness. These improvements contribute not only to the aesthetic appeal of the plated part but also to its increased corrosion resistance and overall durability. They also help in increasing the efficiency of the process, thus lowering the operating cost.
The Role of Intermediates in Achieving a Uniform Zinc Coating:
Achieving a uniform zinc coating thickness is critical for optimal corrosion protection. Variations in coating thickness can lead to premature failure in areas with thinner deposits. Zinc plating intermediates play a crucial role in promoting uniform deposition. Certain intermediates act as leveling agents, preferentially depositing zinc in areas with lower current density, effectively filling in micro-irregularities on the surface. Others work as brighteners, ensuring a consistent and lustrous finish across the entire part. Without these carefully selected and balanced intermediates, it would be significantly more challenging to achieve the consistent, high-quality zinc coatings that are essential for protecting a wide range of metal components in various industries.
Zinc plating intermediates are indispensable components in modern zinc electroplating processes. They influence grain size, brightness, leveling, and overall uniformity of the zinc coating, ultimately enhancing the performance and longevity of the plated part. Understanding the science behind these intermediates and their specific roles is crucial for optimizing the plating process and achieving superior results. When selecting your zinc plating chemicals and additives, remember to consider the specific requirements of your application and choose intermediates that are tailored to your plating bath and desired coating properties. By paying attention to these details, you can ensure a robust, durable, and visually appealing zinc coating that meets the demanding needs of today's industrial applications.
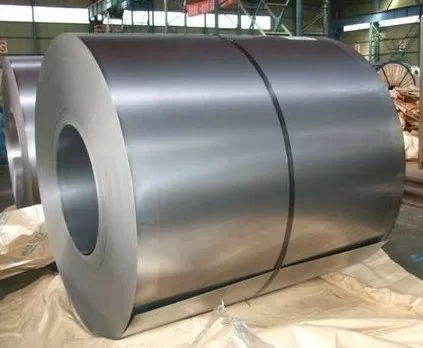
Comments
Post a Comment