Advances in Non-Destructive Testing: The Future of Magnetic Leakage Detection
Table of contents:
Trends in MFL Probe Design and Sensor Signal Optimization
The Importance of Non-Destructive Testing in the Petroleum Industry
Future Trends in MFL Technology for Pipeline Safety
Trends in MFL Probe Design and Sensor Signal Optimization
Recent years have seen significant advancements in the design of MFL probes, focusing on enhanced sensitivity, capability, and durability. One key trend is the integration of optimized sensor technology, which allows for improved detection of minor defects such as micro-cracks or material thinning in ferrous pipelines. By utilizing high-resolution magnetic sensors, MFL probes can capture and interpret leakage fields with exceptional accuracy. Manufacturers are also investing heavily in automation and robotics integration. These innovations not only enhance efficiency but also make it easier to access unreachable or hazardous areas, reducing risk to operators. Advances in data analytics complement this evolution by allowing inspectors to interpret sensor readings more effectively through machine learning algorithms, minimizing false positives and improving the reliability of defect detection. Within the current landscape, wholesale Magnetic Flux Leakage solutions are becoming more accessible, enabling a broader range of industries to adopt these advanced tools for their operations. This makes the selection of a reliable Magnetic Flux Leakage manufacturer critical to achieving the best outcomes for long-term asset management.
The Importance of Non-Destructive Testing in the Petroleum Industry
The petroleum industry relies on strict safety standards, as even small flaws in pipelines or storage tanks can have serious consequences. Non-destructive testing (NDT) methods, especially Magnetic Flux Leakage (MFL) Testing, play a key role in ensuring safety and sustainability. Unlike traditional inspections that can damage materials, MFL testing uses magnetic fields to detect anomalies in pipeline walls and metal structures. This method helps identify corrosion, structural weaknesses, or welding defects early, reducing the risk of leaks or ruptures. Advanced MFL systems with automated probes provide maintenance teams with actionable insights to prevent accidents and minimize downtime. Beyond reducing risks, this technology boosts efficiency, keeping operations smooth. Companies using MFL systems not only enhance safety but also demonstrate a commitment to sustainable production.
Future Trends in MFL Technology for Pipeline Safety
The future of Magnetic Flux Leakage (MFL) technology lies in its ability to tackle the growing challenges of pipeline safety. A key focus is the development of real-time feedback systems, providing engineers with immediate defect data for quick decision-making. As global infrastructure ages, MFL technology is evolving to inspect pipelines with varied geometries, including non-cylindrical or complex shapes. Environmentally friendly innovations, such as energy-efficient probes and eco-conscious materials, are also gaining traction. Companies are enhancing the portability and durability of MFL devices, ensuring even remote sites can access advanced inspection tools. The increasing use of IoT sensors is enabling connected pipelines that automatically notify operators of deterioration. By partnering with an experienced MFL manufacturer offering tailored solutions, businesses can address safety challenges and adopt cutting-edge technology to future-proof operations. Magnetic Flux Leakage remains a critical part of non-destructive testing, delivering precision, speed, and adaptability to meet modern industry needs.
Non-destructive testing using Magnetic Flux Leakage technology continues to break barriers with enhanced defect detection capabilities, efficiency, and adaptability to industry needs. From its critical application in the petroleum sector to the innovations propelling pipeline safety into the future, MFL is a game-changer for industries requiring precise testing solutions. Wholesale Magnetic Flux Leakage solutions and expert Magnetic Flux Leakage manufacturers are making these advancements not only more accessible but also more impactful in safeguarding infrastructure and minimizing operational risks. Staying informed about the latest trends and technologies ensures that businesses are well-equipped to meet safety standards and maintain the integrity of their assets efficiently. When integrated intelligently, these breakthroughs pave the way for a safer industrial landscape.
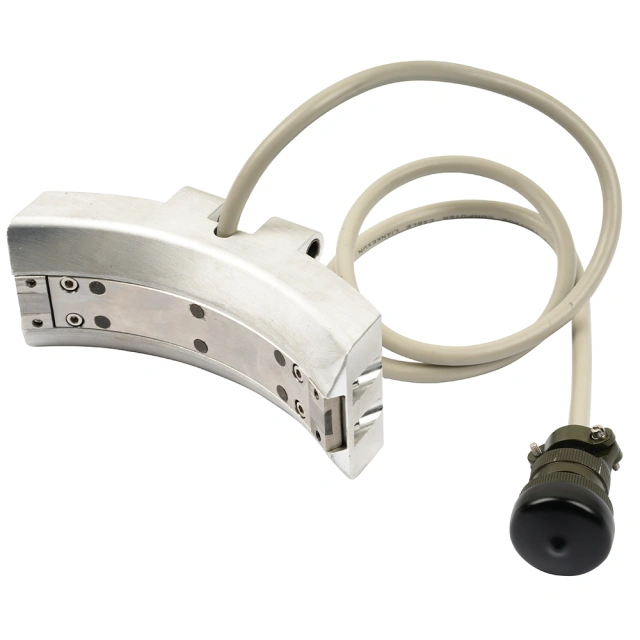
Comments
Post a Comment