The Versatility of Magnetic Drills in Modern Manufacturing
The Versatility of Magnetic Drills in Modern Manufacturing
Exploring the Benefits of Magnetic Drills for On-Site Applications
Safety Considerations When Using Magnetic Drilling Machines
Integrating Magnetic Drills into Your Existing Workflow
Top Magnetic Drills in the Market: Features and Reviews
Exploring the Benefits of Magnetic Drills for On-Site Applications
Magnetic drills bring unparalleled portability and precision to on-site drilling. Unlike stationary machinery like a radial drilling machine or benchtop drill press, magnetic drills are compact and easy to transport, making them an excellent choice for field jobs. Their magnetic base ensures a stable and secure attachment to metal surfaces, reducing the risk of errors while drilling. This feature makes them perfect for construction sites, shipbuilding, and industrial equipment repair, where maneuverability and stability are critical. With the ability to handle a variety of tasks, from drilling small holes to creating larger, precision bores, magnetic drills eliminate the need for bulky drill presses or pillar drill in certain situations. High-end models even offer additional features like variable speeds and automatic feed settings, further improving their utility.
Safety Considerations When Using Magnetic Drilling Machines
Safety is paramount when operating magnetic drilling machines. Their magnetic base provides stability, but proper usage and maintenance are crucial to avoid accidents. Start by ensuring the surface where the drill will attach is clean and free from debris. A dirty surface can compromise the magnet’s hold, making the operation unsafe. Always inspect the drill’s components, especially the magnet and cables, for any damage or wear. When working with heavy materials, use clamps or additional supports to secure them. For environments with low visibility or confined spaces, consider using models with halogen lamps, such as those offered in the DM-20 radial drilling machine series. Remember, magnetic drills operate at high speeds, and proper personal protective equipment (PPE), such as safety goggles and gloves, is non-negotiable. Following these safety protocols ensures efficient and secure operation.
Integrating Magnetic Drills into Your Existing Workflow
Integrating a magnetic drill into your existing manufacturing process can significantly enhance efficiency and productivity. Unlike traditional drill presses or benchtop drill presses, which require you to bring the material to the machine, magnetic drills are portable and can be brought directly to the job site. This capability reduces the time spent on material handling, speeding up project timelines. Magnetic drills are compatible with a wide range of drill bits, such as Annular Cutters, which allow for faster and more precise drilling compared to twist drill bits. Additionally, you can use these drills for tasks traditionally handled by radial drilling machines or pillar drills, such as creating deep or irregularly shaped holes. Modern magnetic drills also come with intelligent features like auto-feed and overload protection, making them an excellent addition to automated workflows. With the ability to integrate seamlessly into diverse manufacturing environments, they prove to be a valuable investment.
Top Magnetic Drills in the Market: Features and Reviews
Choosing the right magnetic drill for your needs is critical. Leading models like the DM-20 radial drilling machine stand out for their robust features and reliability. The DM-20, for instance, boasts a drilling capacity of 20mm and multiple spindle speed settings ranging from 210 to 2000 rpm, making it versatile for different materials. It also includes a cross work table and box table, offering enhanced operational flexibility. Brands such as Evolution and Fein have made significant strides in providing user-friendly, high-performance magnetic drills. Evolution’s models often feature lightweight designs suited for portability, while Fein offers advanced magnetic force monitoring for added safety. Additionally, models equipped with built-in coolant systems, such as the Metabo Mag 50, ensure long-lasting durability and reduced bit wear. User reviews consistently highlight the reliability, precise controls, and extended lifespans of these top-tier machines, making them the go-to choice for professionals.
Magnetic drills are game-changers in modern manufacturing, offering flexibility, efficiency, and safety that surpass traditional alternatives like drill presses or radial drilling machines. Whether you’re working on construction sites, in industrial settings, or handling complex repairs, the unique capabilities of magnetic drills make them a reliable choice for professionals worldwide. By understanding their benefits, safety practices, integration into workflows, and the best models on the market, you can make an informed decision to elevate your operations.
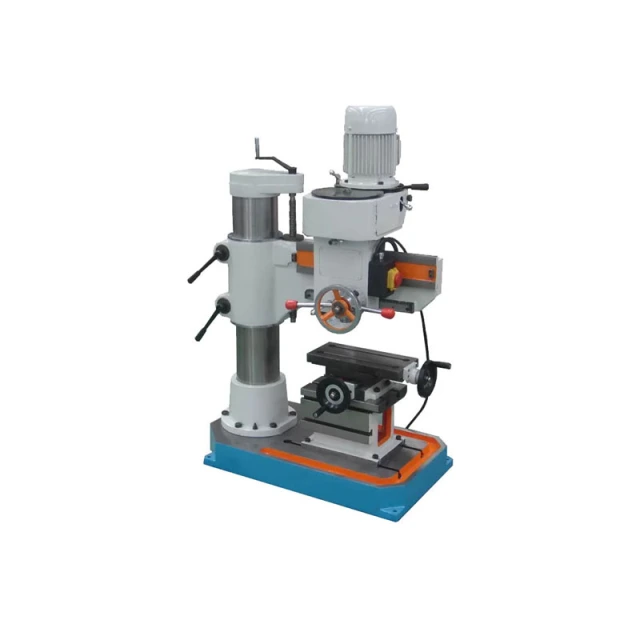
Comments
Post a Comment